


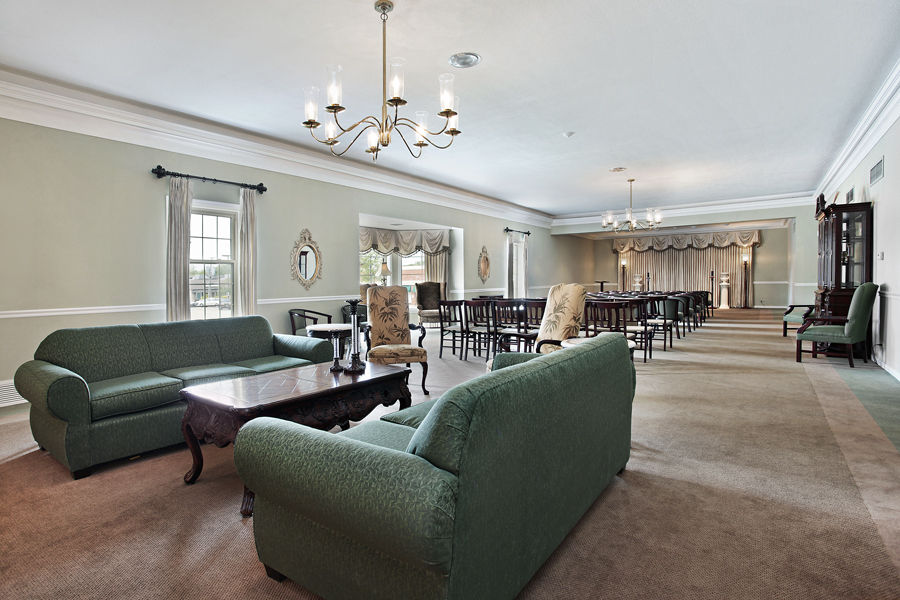


Calcium Chloride Testing
Test 1:
Testing performed in accordance with ASTM F 1869-04 Standard Test Method for measuring Moisture Vapor Emission rate of Concrete Subfloor Using Anhydrous Calcium Chloride and manufacturer’s instructions.
The number of tests required is determined by the square-footage of the project:
-
Three kits are required for the first 1,000 square feet, and
-
One additional test kit for each 1,000 square feet thereafter
-
Test site should be at the same temperature and humidity expected during normal us. If this is not possible, then the test conditions should be 75 Fahrenheit + or - 10 Fahrenheit degrees and at 50% relative humidity + or – 10% relative humidity. Maintain these conditions 48 hours prior to and during testing
-
Prior to test placement, the actual test area shall be clean and free of all foreign substances. All residual, curing compounds, sealers, paints, floor coverings, etc. shall be removed
-
Tests shall not be placed within five feet of nearest external wall
-
Weigh test dish on site prior to start of test. Scale must report to 0.1 grams. Record weight and start time
-
Expose Calcium Chloride and set dish on concrete surface
-
Install test containment dome, (lightly press on the top of the containment dome to assure seal) and allow test to proceed for 60 – 72 hours
-
Retrieve test dish, (lightly press on the top of the containment dome to confirm seal) carefully cutting through containment dome, Close and reseal dish
-
Calculate and report results as “pounds of emission per 1,000 square feet per 24 hours”
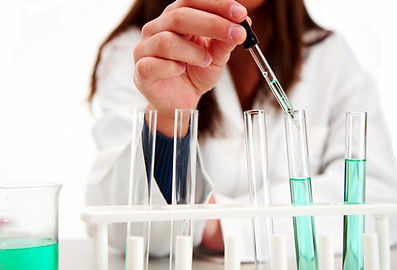

Concrete Relative Humidity Testing
TEST 2:
Testing should be performed in accordance with ASTM F 2170 – 02 Standard Test Method for Determining Relative Humidity in Concrete Floor Slabs Using In Situ Probes
-
The number of tests required is determined by the square-footage of the project:
-
Three kits are required for the first 1,000 square feet, and
-
One additional test kit for each 1,000 square feet thereafter
-
Test site should be at the same temperature and humidity expected during normal us. If this is not possible, then the test conditions should be 75 Fahrenheit + or - 10 Fahrenheit degrees and at 50% relative humidity + or – 10% relative humidity. Maintain these conditions 48 hours prior to and during testing
-
Determine the thickness of the concrete slab, typically from construction documents
-
Utilizing a rotary hammer drill with a carbide-tipped drill bit to drill holes to required depth (for slabs on-grade, depth equal to 40% of the concrete thickness* . i.e. 2.0” deep for a 5” thick slab, or 1.6” deep for a 4” thick slab).
-
Remove dust from the hols using a vacuum cleaner
-
Insert hole liner to bottom of hole. Place rubber stopper into end of liner and seal around liner to concrete at concrete surface with gasketed cover
-
Allow 72 hours to achieve moisture equilibrium within the hole before making relative humidity measurements
-
Remove the sleeve plug and place probe into the sleeve assuring that if reaches the bottom of the test hole
-
Allow ample time for the probe to sit in the test sleeve to achieve moisture equilibrium before taking relative humidity readings.
-
Record the relative humidity and temperature. Also record the location within the structure and depth of the probe tip below the concrete surface.
-
Use the relative humidity probe to measure the ambient air temperature and relative humidity above the slab in the vicinity of the test location.
-
Remove the hole line and fill the hole with a cementicious patching compound.
-
Report any observations that might affect the interpretation of individual measurements such as standing water on the slab, wet coring operations, weather, or ventilating system operations

pH Testing
TEST 3:
Testing should be performed in accordance with ASTM F 710=05 Standard Practice for Preparing Concrete Floors to Receive Resilient Flooring.
Make sure to conduct at same time as vapor emission and relative humidity testing:
-
Place several drops of water onto the concrete surface to form a puddle approximately 1” in diameter
-
Allow the water to set for 60 +/- 5 seconds
-
Dip the pH paper into water and remove immediately. Compare color to chart provided by paper supplier to determine pH reading
-
Record and report results
-
pH Pencil and pH Meters – Follow instrument manufacturer’s instructions
Concrete Testing
At DM Flooring Inspection Services, we know what's under your floor! Concrete and other subfloor types play a key role in how well your flooring system stays in place and performs over time. We often see cases where flooring systems themselves fail because of the interaction between concrete subfloor, adhesives and flooring.
Our industry standard testing will readily identify failure points in your flooring system and our detailed testing and certified written reports will help you determine whether to contact your insurance company, your flooring store or retailer, your contractor or installer, or the manufacturer of flooring.
We have been able to save consumers and businesses millions of dollars and process thousands of claims over the last 25 years in the inspection business.
Here is how it works:
A Bit About Concrete
Some basic information on concrete
Contrary to popular belief, concrete and cement is not the same thing; cement is actually just a component of concrete.
What is concrete?
Concrete is made up of three basic components: water, aggregate (rock, sand, or gravel) and Portland cement.
What is cement?
Cement is a powdery type substance made from a mixture of earth’s materials such as limestone and shale, which is sintered (cause to become solid mass by heating without melting), ground, and mixed with small amounts of calcium sulphate and calcium carbonate.
Cement is activated by water and when mixed with sand and gravel, forms concrete.
Cement is usually grey in color, but white cement can be obtained but is usually more expensive than grey cement.
